Annette Davis
ESR1
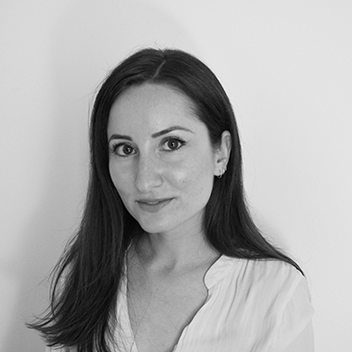
Host university
B1 - School of Architecture La Salle, Ramon Llull UniversitySupervising team
Núria Martí (Supervisor) Ignacio Guillén (Co-Supervisor) Alexandra Paio (Co-Supervisor)Annette is an architect with professional and academic experience in both the UK and abroad. She earned her BSc at the University of Bath, which included a year abroad at the Universidad Europea de Madrid in Spain. During her Master's at the Manchester School of Architecture, she pursued her passion for improving social housing through her project Rethinking the Highrise. The project highlighted the need for both private outdoor space and communal green areas in high-rise social housing, proposing modular stacked dwellings as a solution. She completed her RIBA Part 3 qualification at the University of Westminster in 2019.
Annette’s professional experience of four years spans a wide range of residential, public realm, educational and commercial projects in Melbourne, Australia and at several award-winning London practices. In addition to her professional work, Annette has been actively involved in sustainability and volunteer initiatives. She played a key role in sustainability groups at previous practices, volunteered as an RIBA Ambassador in 2019, and is involved with the Architects Climate Action Network (ACAN) in Spain and the UK. Her current doctoral research aims to further the circular economy transition in housing through the integration of industrialised construction with design for disassembly.
Publications
Davis, A., van Bortel, G., & Martí Audí, N. (2025). Circular Industrialised Housing: Insights from Solar Decathlon Europe 2022. Sustainability, 17(2), 638.
Davis, A., Quintana-Gallardo, A., Martí Audí, N., & Guillén Guillamón, I. (2025). The impact of lifespan assumptions in LCA: Comparing the replacement of building parts versus building layers—A housing case study. Energy and Buildings, 326, 115050.
January, 24, 2024
July, 03, 2023
July, 18, 2022
March, 21, 2022
December, 14, 2021
September, 14, 2021
THE CIRCULAR TRANSITION IN HOUSING: FROM THEORY TO PRACTICE
The current lack of sustainable and affordable housing is a global issue which has reached a crisis point. The negative environmental impacts of the energy and materials consumed during the whole life cycle of housing is not typically considered, whilst in terms of affordability there is a lack of social and affordable housing for growing urban populations. Furthermore, residential buildings account for an average of 75% of the EU building stock, making the role of the housing sector in this twin crisis even more critical.
Transitioning to the circular economy is high on the EU agenda and shows potential to improve both environmental sustainability and affordability of housing in the long term. However, strategies to implement circular construction, supporting the systematic reuse of buildings materials, are largely theoretical and rarely fully implemented in permanent housing.
This project responds to a lack of knowledge and guidance for stakeholders to achieve 'circular housing' at the building scale by providing practical evidence-based information centring on two key approaches: industrialised construction (known as Modern Methods of Construction in the UK) in combination with design for disassembly.
The expected outputs are (1) a circular process framework and (2) interdisciplinary guidelines covering the “dos and don’ts” of circular construction aimed at housing providers, designers, contractors, and local-level policymakers. The outputs draw on the findings from a Systematic Literature Review, Life Cycle Assessment study, off-site factory and on-site disassembly/reassembly observations, interviews with industry experts and policymakers, and workshops to validate the outputs.
BRIDGING THE GAP BETWEEN THEORY TO PRACTICE: ACHIEVING CIRCULAR SOCIAL AND AFFORDABLE HOUSING THROUGH DESIGN FOR DISASSEMBLY AND INDUSTRIALISED CONSTRUCTION
The current lack of sustainable and affordable housing is a global issue which has reached a crisis point. The negative environmental impacts of the energy and materials consumed during the whole life cycle of housing is not typically considered, whilst in terms of affordability there is a lack of social and affordable housing for growing urban populations. Furthermore, residential buildings account for an average of 75% of the EU building stock, making the role of housing in the twin crises even more critical.
An important issue to address these challenges is resource inefficiency in housing, construction not only contributes to nearly 40% of global energy-related CO2 emissions; half of the world’s materials are extracted for the construction industry and over a third of all waste in the EU is generated by construction and demolition. Transitioning to the circular economy can improve both environmental sustainability and affordability of housing in the long term. Designing buildings to be disassembled plays an instrumental in realising the circular transition, however, it is rarely fully implemented in permanent housing.
This project responds to a lack of knowledge and guidance for industry stakeholders to achieve 'circular' social and affordable housing at the building scale by providing practical evidence-based information centring on two key approaches: industrialised construction (known as Modern Methods of Construction in the UK) in combination with design for disassembly.
The expected outputs are interdisciplinary guidelines aimed at (1) housing providers, (2) designers and (3) housing manufacturers in how to apply circular principles to affordable and social housing using disassembly and industrialised methods at key milestones. The guidelines will be validated by collaborating partners and cover best practices and lessons learnt for circular housing based on an extensive literature review, the development of an adapted Life Cycle Assessment methodology, and observations and interviews from academia and industry.
Reference documents
Affordable and Social Housing in the Circular Economy Transition: Industrialised Construction and Design for Disassembly
The current lack of sustainable and affordable housing is a global issue which has reached a crisis point. The design, construction, maintenance, and deconstruction of housing typically does not consider life cycle thinking, which has negative environmental impacts. In tandem, there is a lack of social and affordable housing, the latter of which is becoming increasingly unaffordable. A key issue to address these challenges is resource inefficiency in housing, construction not only accounts for nearly 40% of global energy-related CO2 emissions; over a third of all waste in the EU is generated by construction and demolition.
This project addresses a lack of knowledge in how to provide environmentally sustainable housing that is not disproportionally expensive. This will be achieved through investigating how Design for Disassembly (DfD) in combination with Industrialised Construction (IC) can provide sustainable housing based on Circular Economy principles. DfD is the design and planning for the future disassembly of a building, which can be used to minimise the extraction of raw materials by prolonging the building lifespan and facilitating reuse and recycling at the end-of-life stage. Within this project, DfD principles are combined with the Shearing Layers concept, separating building elements to account for their varying life spans. This facilitates increased flexibility and adaptability, optimised maintenance, retention of heritage, and the possibility to easily relocate an entire building. These benefits can be scaled-up when paired with IC to deliver social and affordable housing through economies of scale. Measuring the environmental impacts of housing designed for disassembly using Life Cycle Assessment (LCA) presents additional unresolved issues. Despite the potential benefits, DfD in combination with IC is not commonly implemented in practice within housing. This project is therefore based on the hypothesis that DfD combined with IC and integrated with Shearing Layers can deliver sustainable and affordable housing.
The aim of this project is to provide strategies for key stakeholders in the delivery of affordable housing to increase the adoption of Design for Disassembly in combination with Industrialised Construction.
This will be achieved through interviews with experts from industry (contractors, architects, and sustainability consultants), academia, and public and private housing providers to gain their knowledge as to best practices and barriers preventing adoption. Three types of housing will be included in the scope of research: affordable, social, and emergency housing. The Shearing Layers concept will be applied to the cradle-to-cradle LCA of three in-depth case studies to quantify the environmental impacts of housing designed for disassembly. The expected project outcomes are three guidelines aimed at designers, contractors, and housing providers, in addition to a tested LCA methodology for projects that plan to implement DfD.
Reference documents

Key concepts | Achieving circular goals in housing: Design for Disassembly in combination with Industrialised Construction
ViewIndustrialising Housing to Meet Circular Goals:
A cradle-to-cradle assessment in combination with Design for Disassembly and Shearing Layers
The climate and housing crises are putting increasing pressure on the construction industry to shift from the current paradigm to a more sustainable and affordable one. Construction accounts for nearly 40% of global energy-related CO2 emissions, whilst over a third of all waste in the EU is generated by construction and demolition. Additionally, advancements in energy efficiency and reduced operational carbon have exposed the urgent need reduce the extraction of raw materials and embodied carbon to achieve net zero by 2050. In tandem, there is a lack of social and affordable housing, the latter of which is becoming increasingly unaffordable. To address these challenges, the industry must move away from the linear “take-make-waste” model that has underpinned development to a Circular Economy (CE) approach, which decouples growth from the consumption of finite resources. A circular building system provides the opportunity to improve the affordability of housing whilst simultaneously improving environmental sustainability.
Industrialised Construction (IC) - or Modern Methods of Construction (MMC) - is a broad term encompassing the systematic and controlled production of buildings; it is increasingly associated with industry 4.0 and merging with ICTs such as BIM to support an integrated project team and document information for all building life-cycle stages. IC can be combined with economies of scale to provide social and affordable housing: reducing construction time, improving build quality, and reducing costs. Production of industrialised housing can take place in factories either off-site or in temporary on-site hubs. It is expected that a significant proportion of housing in the coming decades across Europe will be built in such factories, and sustainable homes will be mass customised from range of standard elements. Both IC and CE principles consider buildings as a product rather than a one-off prototype. These two schools of thought intersect in practice through Design for Disassembly (DfD) where demountable standardised elements are easily adapted, reused, repaired, recycled, or relocated.
A circular approach is of high priority in the EU and globally as highlighted by the Circular Economy Action Plan, and changes in leading Green Building assessments and the new Europe-wide framework Level(s). These assessments are increasingly reliant on quantitative data and cradle-to-cradle Life Cycle Analysis (LCA) to measure resource and energy efficiency. However, applying the current Whole Building LCA method to industrialised housing and DfD is an unresolved issue. The standard LCA method assumes a 60-year life span for the entire building, that does not account the varying lifespans of different building layers. In addition, this does not support the comparison of a range of large building elements to inform design decisions in mass customised housing. These are crucial issues to address not only to appropriately assess the sustainability of industrialised housing, but to set appropriate governmental targets.
The aim of this project is therefore twofold: to investigate how Design for Disassembly (DfD) can provide circular sustainability solutions in housing and strategies for increased adoption at the building and policy levels.
Within this project, a new method is proposed to assess the sustainability of housing designed to be disassembled. This will be based on a cradle-to-cradle LCA using Building Information Modelling (BIM), which will incorporate holistic indicators in combination with the Shearing Layers concept, with different assumed lifespans for each layer. This will enable technical stakeholders to make better informed design decisions throughout all building stages and provide sustainable solutions based on more accurate information, within a less time-consuming process. This will be achieved through testing the proposed methodology on both research and industry projects with Universitat Politècnica de València (UPV) and construction company Grupo Casais. The expected outcome of this project is an outline methodology to be used in industry, which will include a roadmap and recommendations to achieve this.
Keywords: Industrialised Construction (IC), Building Information Modelling (BIM), Design for Disassembly (DfD), Life Cycle Analysis (LCA), Cradle-to-cradle (C2C), Shearing Layers.
Reference documents
A framework for sustainable and affordable housing using Industrialised Construction
Industrialised Construction (IC) is a broad term which encompasses systematic and controlled production. IC is no longer synonymous with mass production and prefabrication, and novel methods are more often taking place on site. Today IC is used to deliver customer-oriented housing through mass customisation and is increasingly used in combination with ICTs such as BIM to implement lean methods. Recent advancements in IC and ICTs have created a paradigm shift in the Architecture Engineering and Construction (AEC) industry, with a different view of the building lifetime that goes beyond practical completion.
There is growing attention on utilising IC to provide innovative solutions for today’s housing challenges in sustainability and affordability, in addition to managing building complexity and coordination with various fields. Recent ambitious EU targets to deliver Net Zero Energy Buildings and to incorporate circular economy have put increasing pressure on the construction industry to shift from the current paradigm to a more sustainable one. When used in conjunction with economies of scale IC can improve build quality, minimise waste, and reduce cost and time of construction. However, there needs to be a greater understanding of IC by both technical and non-technical stakeholders for its benefits to be fully realised.
This project will investigate the benefits that a combination of industrialised methods and ICTs can provide in delivering sustainable and affordable housing. The research will seek to establish methods suitable for housing within a BIM-centric framework, demonstrating the benefits in terms of sustainability and affordability supported with case studies in collaboration with construction company Grupo Casais. The methodology will include establishing indicators in conjunction with Life Cycle Analysis. This will cover all building stages, including beyond the end-of life-stage for a circular approach. The proposed outputs will include a framework and guidelines for actors involved in the delivery of housing.
A framework for sustainable development of housing using Industrialised Construction
Industrialised Construction (IC) is a broad term which encompasses systematic and controlled production. IC is no longer synonymous with mass production and prefabrication, and novel methods are more often taking place on site. Today IC is used to deliver customer-oriented housing through mass customisation and is increasingly used in combination with ICTs such as BIM to implement lean methods. IC raises the question of what constitutes a ‘home’; arguably some of the innovative methods intended for other purposes such as travel, military use, or product design, which have been adapted to housing are inherently unsuitable.
There is growing attention on utilising IC to provide innovative solutions for today’s housing challenges in sustainability and affordability, in addition to managing building complexity and coordination with various fields. Recent ambitious EU targets to deliver Net Zero Energy Buildings and to incorporate circular economy have put increasing pressure on the construction industry to shift from the current paradigm to a more sustainable one. When used in conjunction with economies of scale IC can improve build quality, minimise waste, and reduce cost and time of construction. However, there needs to be a greater understanding of IC by both technical and non-technical stakeholders for its benefits to be fully realised.
This project will investigate the benefits that a combination of industrialised methods and ICTs can provide in delivering sustainable and affordable housing. The research will seek to establish current methods suitable for housing within a framework, demonstrating the benefits in terms of sustainable development supported with case studies in collaboration with construction company Grupo Casais. Using a systems approach, the methodology will include establishing indicators in conjunction with Life Cycle Analysis (LCA). The analysis will cover all building stages, including beyond the end-of life-stage for a circular approach in line with the Level(s) framework. The proposed outputs will include a framework and guidelines for actors involved in the delivery of housing.
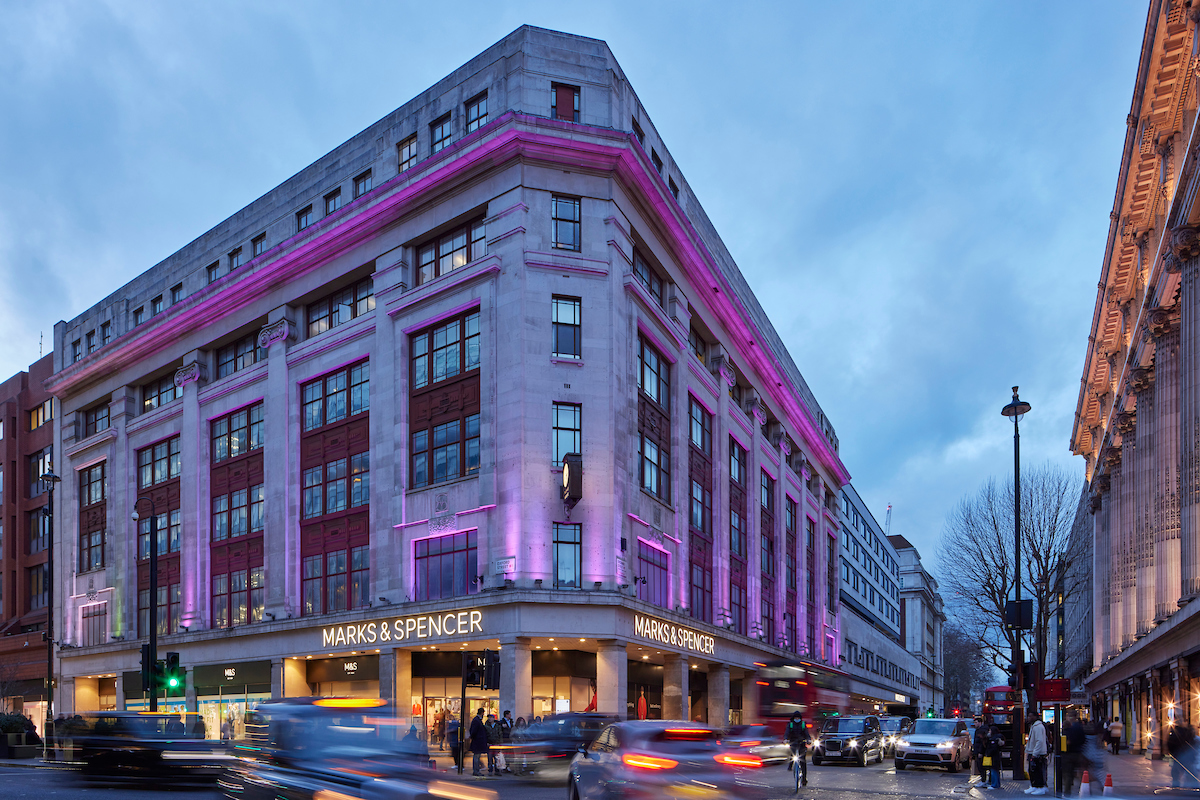
Let’s talk embodied carbon
Posted on 26-07-2023
Reflections
Read more ->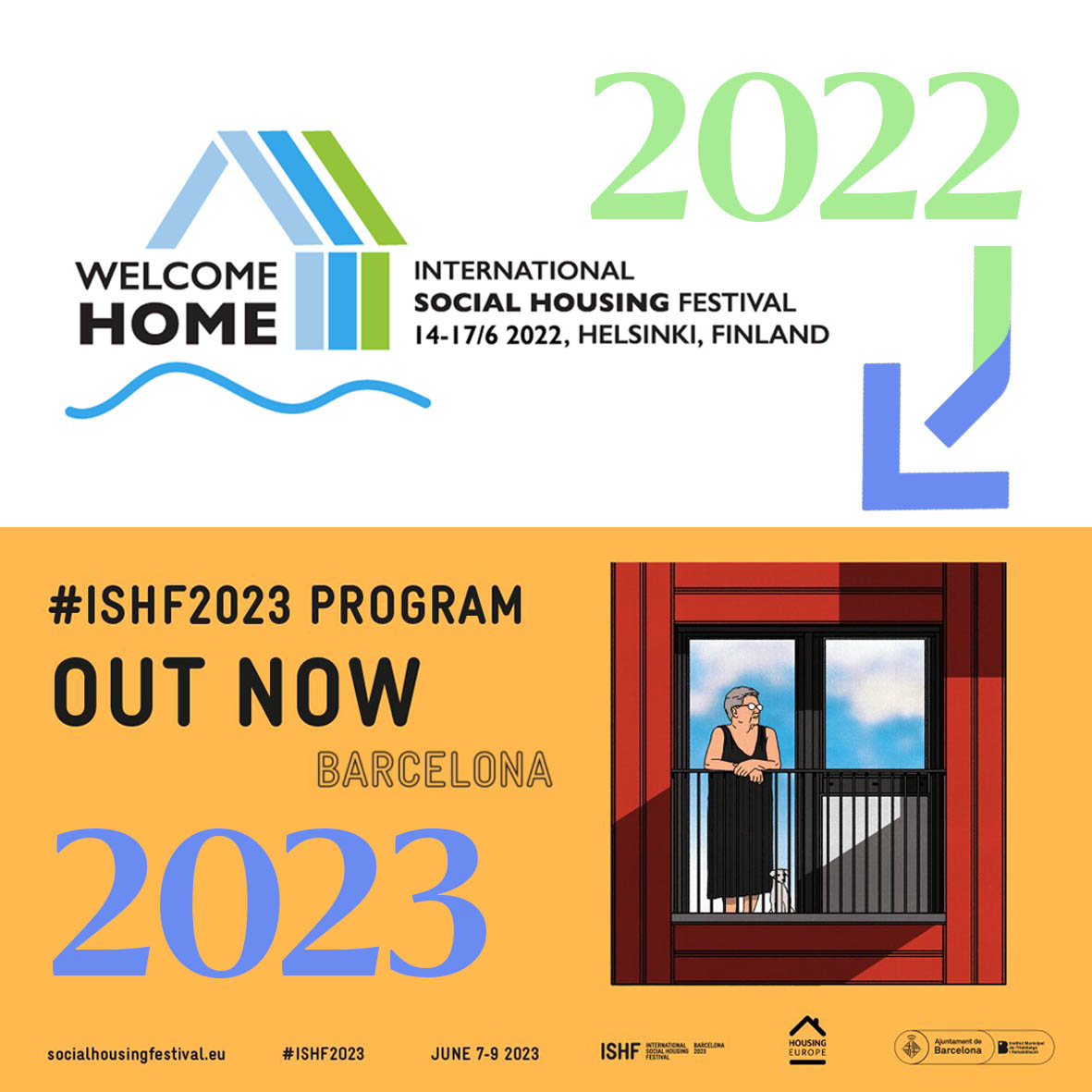
Celebrating Social Housing
Posted on 29-05-2023
Conferences
Read more ->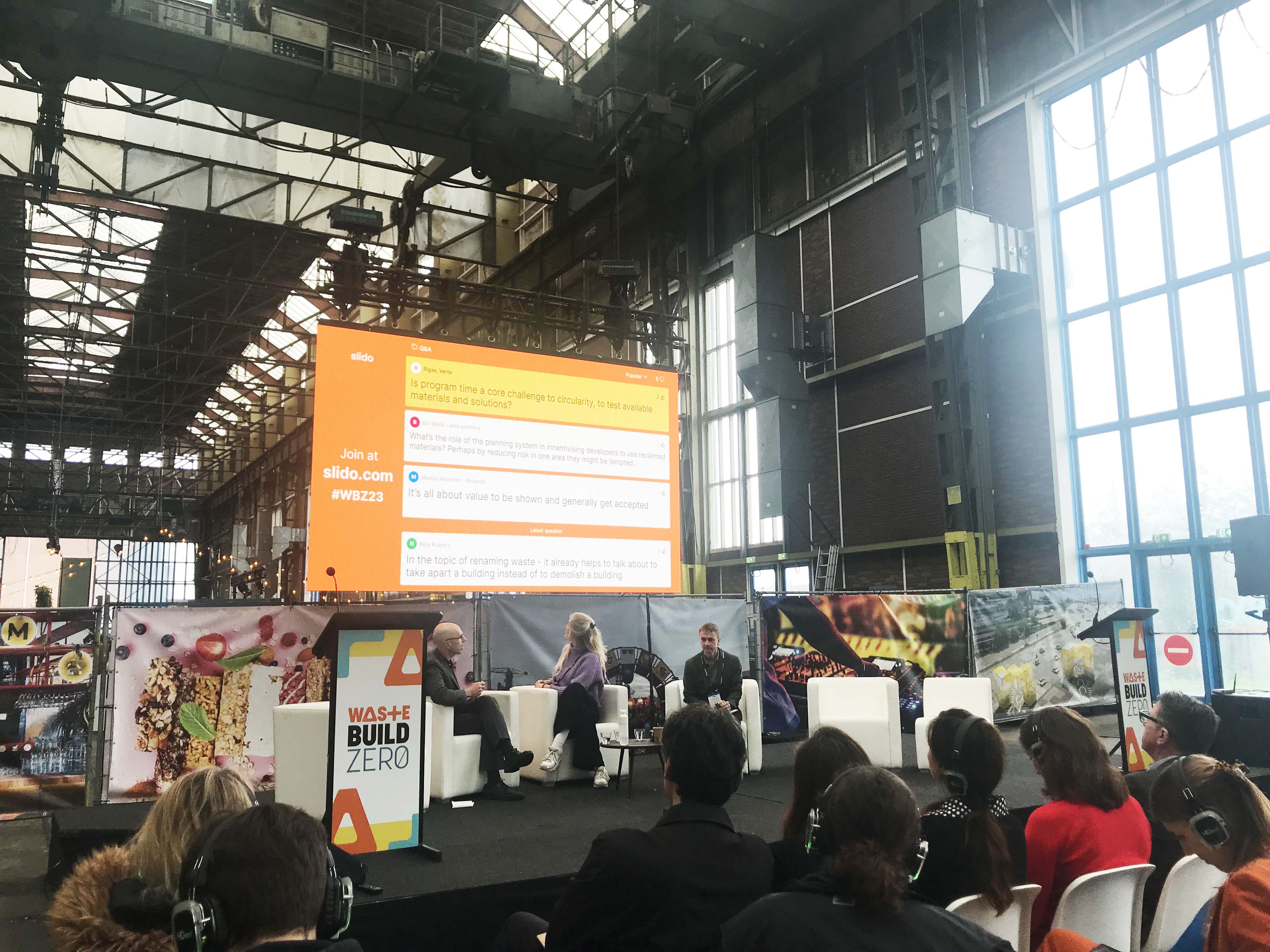
WasteBuild Zero conference in Amsterdam
Posted on 18-05-2023
Conferences, Secondments
Read more ->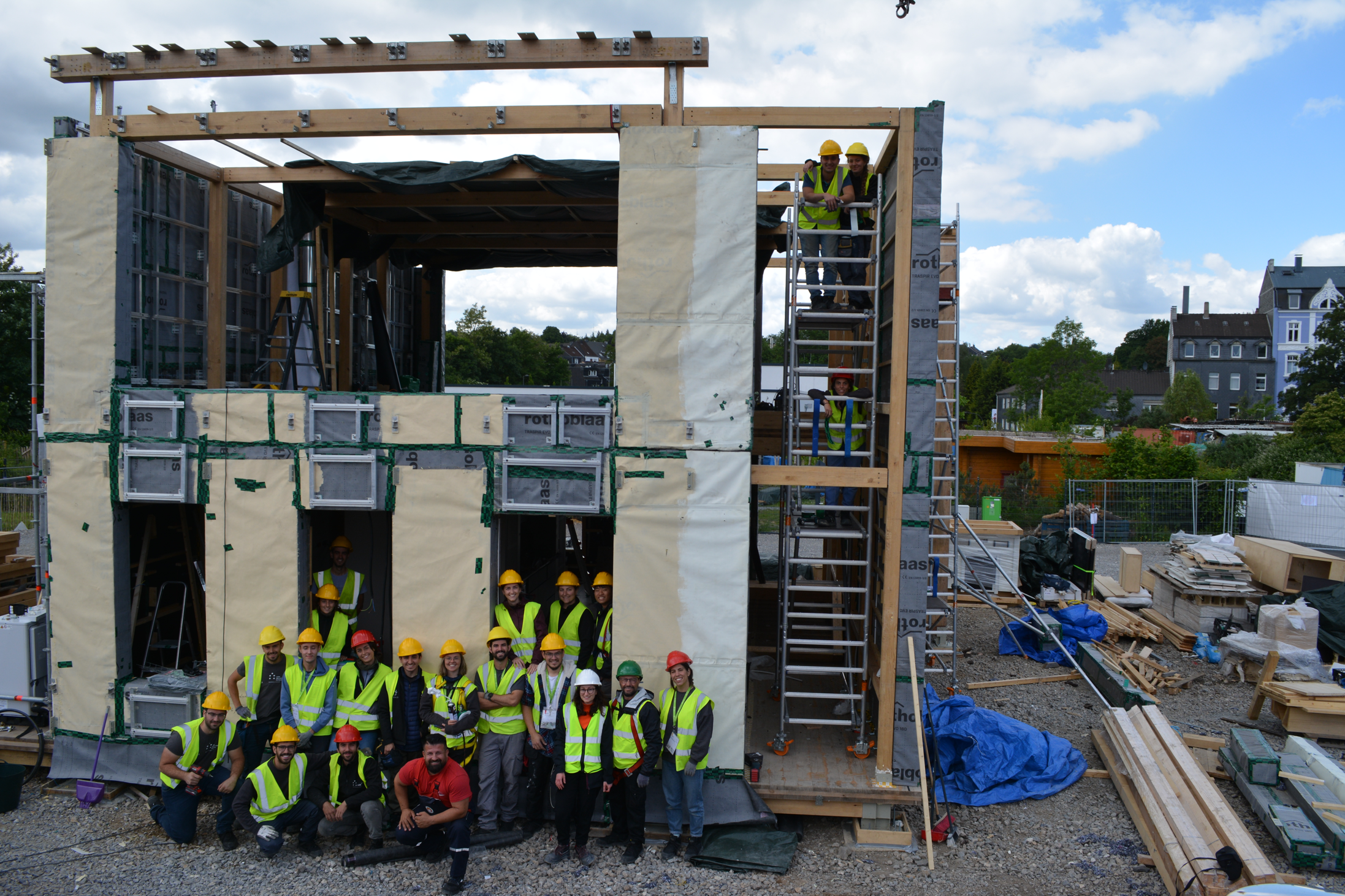
Solar Decathlon Competition and LCA | Secondment with UPV
Posted on 27-10-2022
Secondments
Read more ->ESRs visit to the Casais Group in Portugal
Posted on 09-03-2022
Reflections
Read more ->
Nicosia: The divided city
Posted on 13-12-2021
Summer schools, Reflections
Read more ->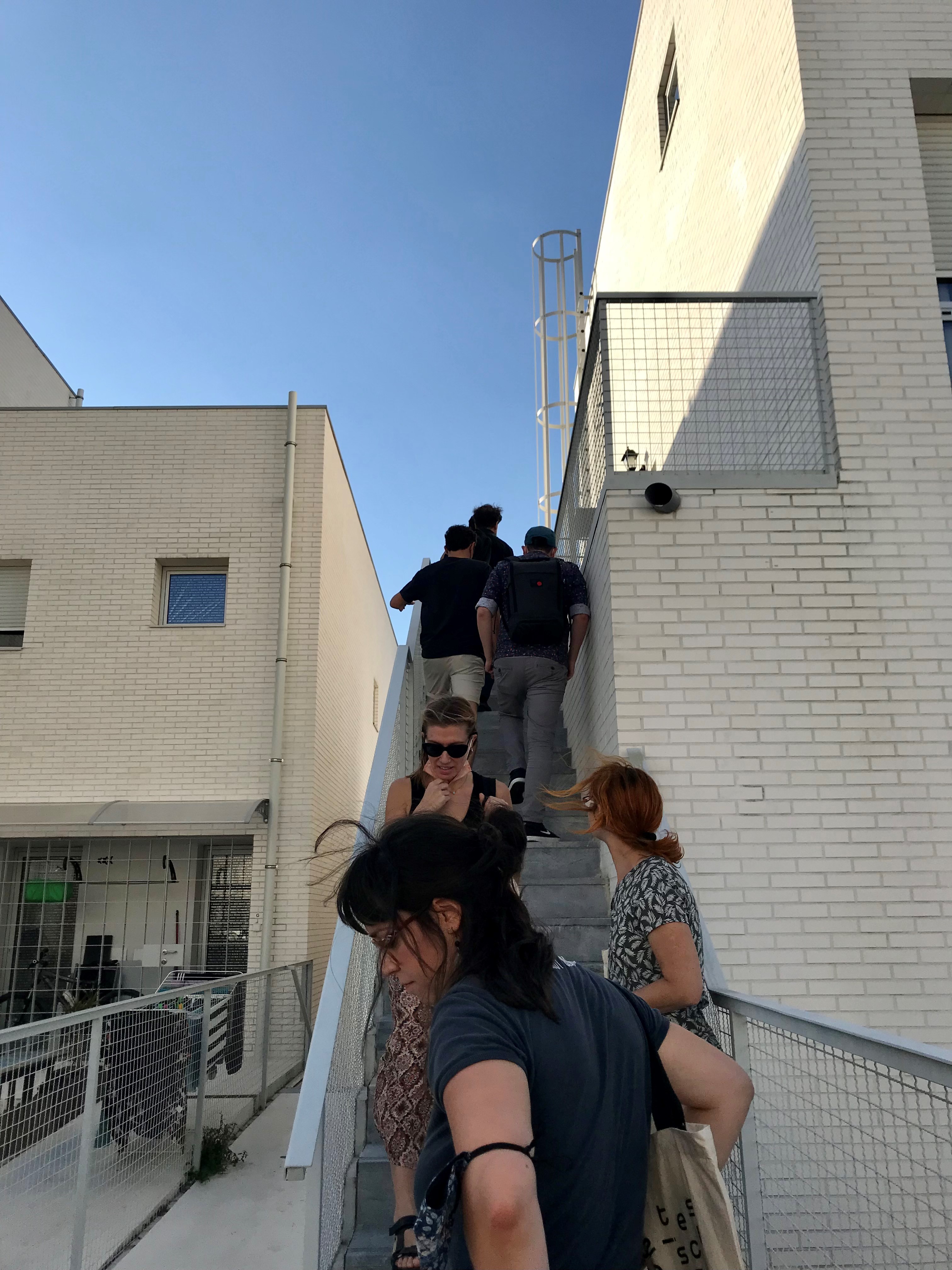
Links between sustainability and BIM
Posted on 10-12-2021
Workshops, Reflections
Read more ->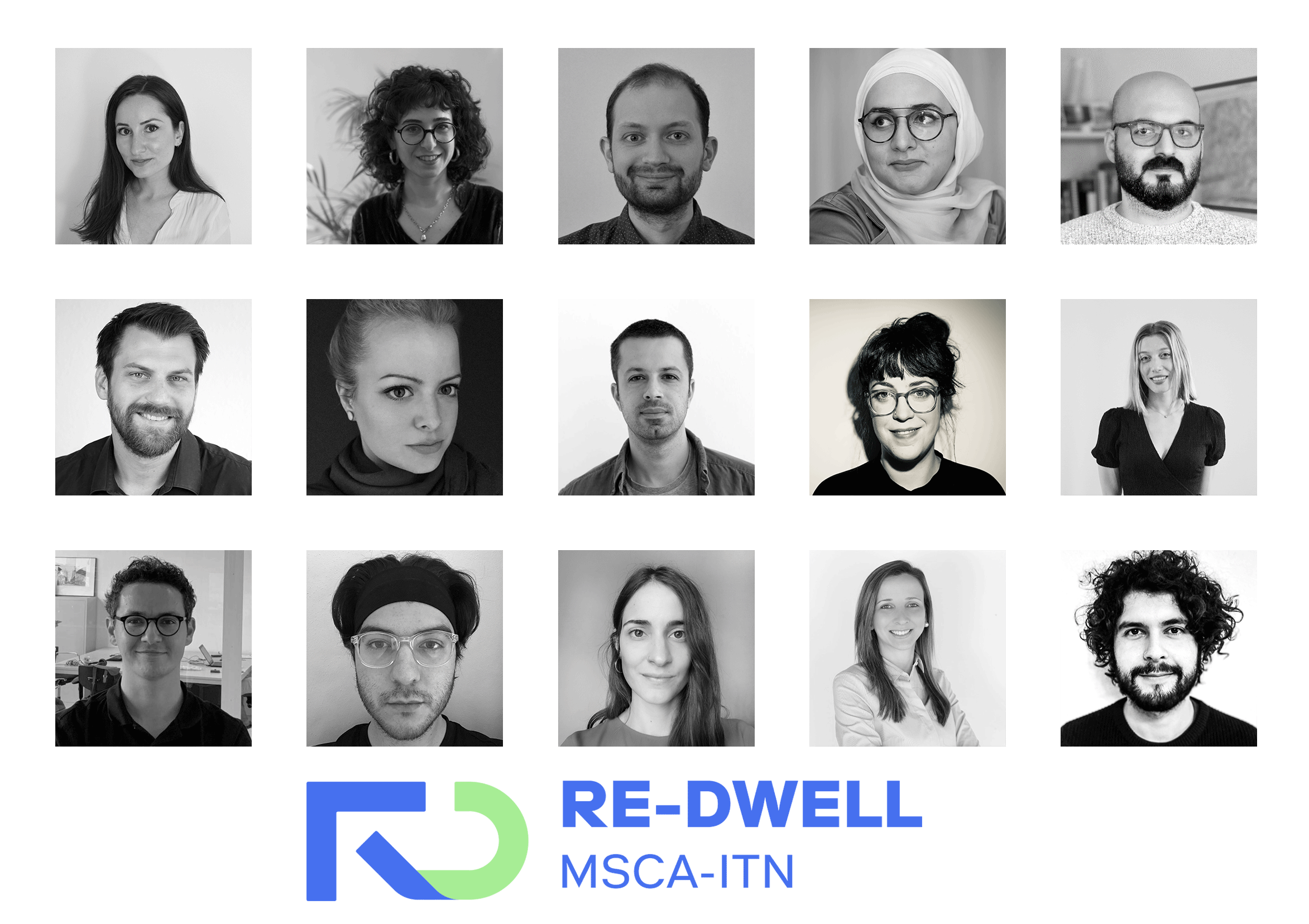
Embracing transdisciplinarity
Posted on 15-07-2021
Workshops
Read more ->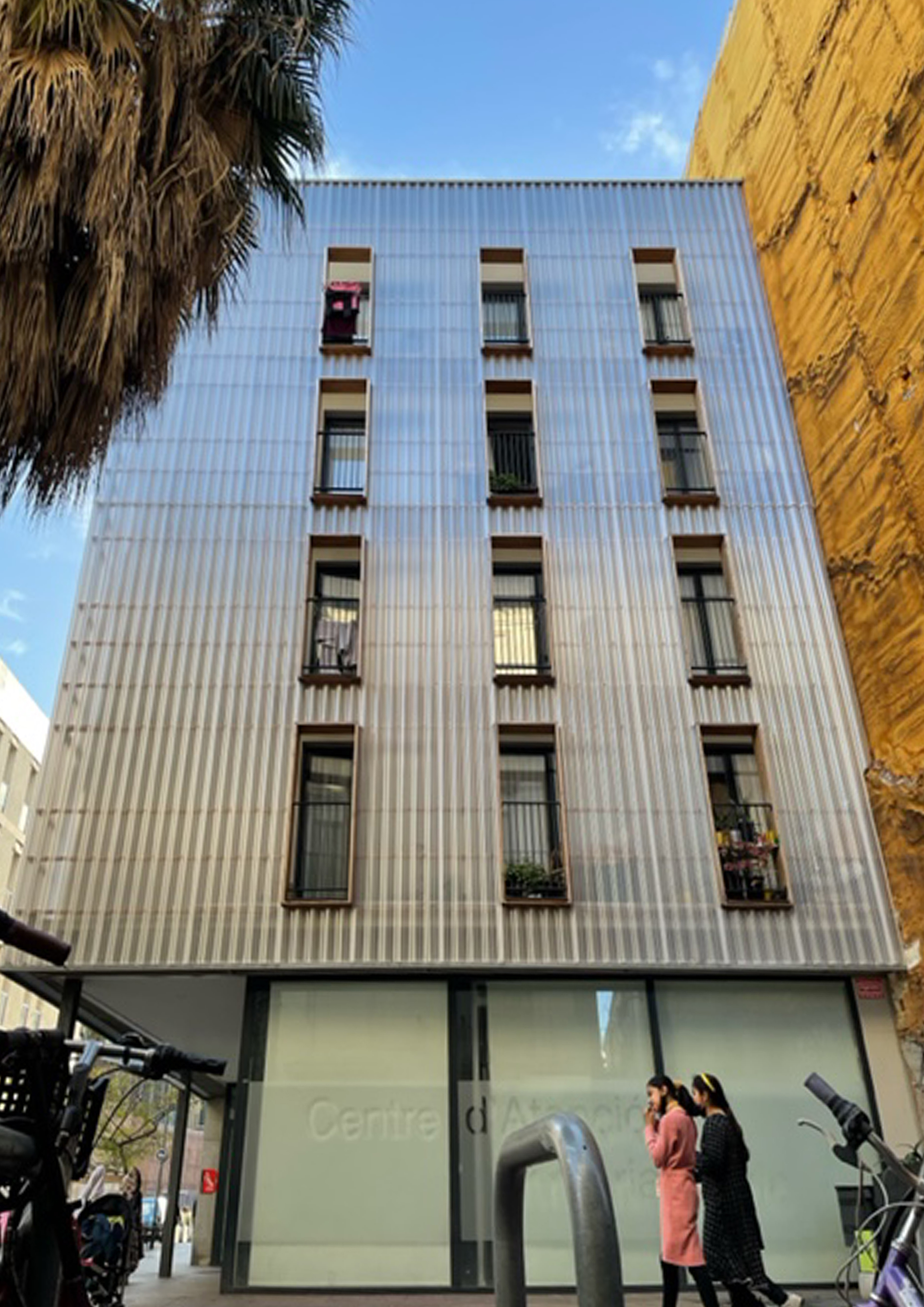
APROP | Temporary social housing for people at risk to residential exclusion
Created on 09-10-2024
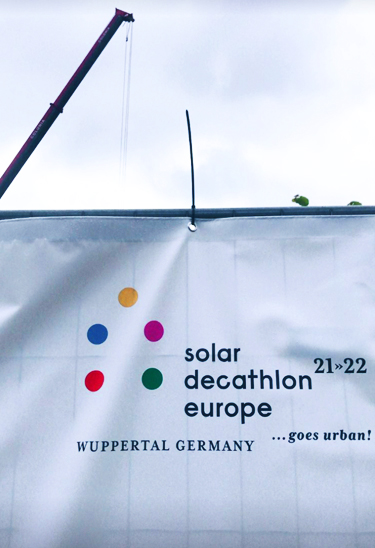
Solar Decathlon Europe 2022
Created on 21-11-2024

WikiHouse: South Yorkshire Housing Association
Created on 16-10-2024
BIM
Circular Economy
Design for Disassembly
Industrialised Construction
Life Cycle Assessment
Transdisciplinarity
Area: Design, planning and building
Created on 16-02-2022
Read more ->Area: Design, planning and building
Created on 30-09-2024
Read more ->Area: Design, planning and building
Created on 18-10-2023
Read more ->Area: Design, planning and building
Created on 09-11-2023
Read more ->Area: Design, planning and building
Created on 30-09-2024
Read more ->Area: Community participation
Created on 05-07-2022
Read more ->Davis, A. (2024). Circular Housing: Insights from Solar Decathlon Europe 2022. In European Network for Housing Research (ENHR) Conference 2024 [Poster Presentation]. Delft, the Netherlands.
Posted on 30-06-2025
Conference
Read more ->