Solar Decathlon Europe 2022
Created on 13-11-2023 | Updated on 21-11-2024
Solar Decathlon Europe (SDE) is a university competition where student-led teams undertake the challenge of designing and constructing highly innovative and environmentally sustainable 1:1 scale House Demonstration Units (HDU). Originally launched in the USA in 2002, the competition expanded its reach to Europe in 2010 (SDE, 2019). Competing teams typically involve research groups within universities and are sponsored by industry partners, such as contractors and product manufacturers. After the competition, the homes become accessible to the public, featuring guided tours that highlight the cutting-edge advancements in sustainable housing.
Although the competition’s primary design challenge focuses on minimising operational carbon, participating teams must also address the path towards achieving a climate-neutral building stock. The construction task requires teams to create prefabricated building systems, assemble their HDU at a site in their home country, disassemble it, then transport and reassemble it within just two weeks at the competition site, known as the Solar Campus. This means design for disassembly and circularity are integral to the competition, making it a unique opportunity to demonstrate how permanent housing (as opposed to temporary or emergency housing) can be designed to reduce embodied carbon throughout the whole life cycle and discourage potential future demolition.
The SDE-2022 edition took place in Wuppertal, Germany under the theme “SDE Goes Urban!” Sixteen teams from countries including Czechia, France, Germany, Hungary, Netherlands, Romania, Spain, Sweden, Taiwan and Turkey took part in the build challenge. Teams were awarded points in ten categories, covering environmental and social sustainability aspects, as well as affordability and viability. This case study provides an overview of the SDE competition in 2022, which was attended by the author on-site. More information about the visit can be found in this blog post.
Architect(s)
16 competing universities
Location
Wuppertal, Germany
Project (year)
2021-2022
Construction (year)
2022
Housing type
multifamily housing
Urban context
City centre
Construction system
Prefabricated sustainable homes designed and built to be disassembled and relocated for reassembly
Status
Built
Description
Relationship to urban environment
The SDE 2022 competition called for innovative urban housing solutions within existing contexts, allowing teams to choose from one of three scenarios: (1) a vertical extension adding additional storeys, (2) closing gaps between buildings, or (3) a horizontal extension. Among the sixteen built projects, eleven were top-ups, four were in-fill, and one was a horizontal extension. Some teams opted for a top-up solution for the existing Café Ada site in Wuppertal, whilst others produced solutions tailored to a local context of their home country. Despite the diverse origins of the projects, all of them had to be transported and operated at the Solar Campus in Wuppertal, Germany. Table 1 shows the results of the competition, which was won by team RoofKIT from the Karlsruhe Institute of Technology. Note that the third place was tied between teams SUM from TU Delft and Aura from Grenoble School or Architecture.
Innovative aspects of the housing design/building
As documented in the competition Source Book (Voss & Simon, 2022), the teams developed various innovative biological, low-carbon, and circular materials and products from various other sectors, such as mycelium bound insulation, sea grass, recycled newspapers, jeans for insulation, and recycled yoghurt pots for kitchen and bathroom joinery. Chalmers University’s Team Sweden experimented with 3D printed cellulose whilst team X4S from Biberach University of Applied Sciences used tubular thin film photovoltaics, originally developed for large-scale use in agriculture, as pergola roofing. Innovative layouts included tessellating modules to provide multiple configurations, and highly efficient living units for multiple households (SDE, 2022).
Construction characteristics, materials and processes
All teams used Industrialised Construction (also known as Modern Methods of Construction in the UK) to varying degrees to prefabricate their buildings in their home countries. Construction included timber-based 3D modular and 2D panelised elements, and the competition also required the use of BIM to model the designs. To be able to disassemble and reassemble the HDUs they had to avoid the use of glues and wet sealants and instead join the building parts using various forms of reversible connections. Strategies included interlocking wood jointing, steel plates and footings, tapes, and mechanical joints such as screws, rivets, and bolts (Voss & Simon, 2022). These joining methods were designed to withstand water-ingress as well as airtightness, which was tested using the blower door test.
Energy performance characteristics
High energy efficiency performance and the production of on-site renewable energy were critical design aspects of the competition. All homes were designed to use electricity as the sole energy source for energy services and were powered by air- and ground-source heat pumps, and photovoltaic panels were integrated both horizontally on roofs and vertically on façades, depending on whether the project responded as an infill or top-up solution (Voss & Simon, 2022). Nine HDUs met the Passive House standard and included innovative passive strategies, such as solar chimneys, which were implemented by five teams, including Azalea from the Polytechnic University of València. Eight of the sixteen teams were chosen to remain on-site for an additional 3-5 years after the competition as Living Labs to provide in-use research data (University of Wuppertal, 2022).
Involvement of other stakeholders
The competition incorporates a level of entrepreneurship, with teams encouraged to forge partnerships and gain sponsorship from various industry partners. This provided teams with a mixture of financial support, in-kind services, or donations of materials and products. The extent of collaboration with partners and sponsors varied across the teams: these were formed not only with contractors and product suppliers, but in some cases with housing associations and local municipalities as well. The involvement of stakeholders from different fields not only fostered collaboration between fields, but brought about innovative construction solutions, bridging the gap between academia and industry.
Alignment with project research areas
Solar Decathlon Europe is an architectural competition for sustainable housing which focuses on the quality of design and construction. Financing is integral to the realisation of the projects and is managed by the student teams. Community participation is not a requirement of the competition and the HDU’s on the Solar Campus do not provide housing for the public.
Design, planning and building (Highly related)
The competition is based on the design and build challenges that focus on the architecture and engineering dimensions with consideration for urban design and potentially responding to different contexts. Detailed design criteria are assessed within the Architecture and Engineering & Construction contests and include aspects such as aesthetic design quality, structure, durability, coherence of the design, and energy performance (SDE, 2021)
Policy and Financing (Moderately related)
SDE 2022 provided financial support of €100,000 as base funding. Teams were then responsible for raising additional funds though sponsorship and donations. Regarding the concept design, affordability was taken seriously by the teams, whose proposals also included considered business cases for affordable and social housing solutions.
Community participation (Not related)
Solar Decathlon was not designed to be a participatory project. However, due to the high media coverage, the competition tends to generate a considerable amount of public interest. An additional objective of the competition is to generate social awareness and educate the general public to understand the SDE topics and the need for an energy transition in the built environment.
* This diagram is for illustrative purposes only based on the author’s interpretation of the above case study
Alignment with SDGs
The competition is “completely in the spirit of sustainable development” as the competition centres on developing housing solutions reflecting the needs of future generations (Voss & Simon, 2022). Most teams directly aligned their proposals to the UN Sustainable Development Goals within their submitted project manuals. The Solar Decathlon Europe competition demonstrates particular alignment with the following targets:
7a “By 2030, enhance international cooperation to facilitate access to clean energy research and technology, including renewable energy, energy efficiency and advanced and cleaner fossil-fuel technology, and promote investment in energy infrastructure and clean energy technology” | The competition was founded on developing highly energy efficient housing based on renewable energy.
11.1 “By 2030, ensure access for all to adequate, safe and affordable housing and basic services and upgrade slums” | With “housing becoming scarcer and more unaffordable for large numbers of people” (Voss & Simon, 2022) the teams proposals addressed a lack of adequate and affordable housing in urban contexts.
11.6 “By 2030, reduce the adverse per capita environmental impact of cities, including by paying special attention to air quality and municipal and other waste management” | The teams provided circular housing solutions that minimises waste in both the short and long term.
13.3 “Improve education, awareness-raising and human and institutional capacity on climate change mitigation, adaptation, impact reduction and early warning” | The competition improves knowledge around climate change mitigation in the built environment for a new generation of young design professionals and participating industry partners through the design and build challenges. The innovative solutions are showcased with open events to raise awareness internationally with the general public.
References
SDE. (2019). The SDE story. https://solardecathlon.eu/the-sde-story/
SDE. (2021). Solar Decathlon Europe goes urban Wuppertal Germany - rules version 2.1. https://solardecathlon.eu/wp/wp-content/uploads/2021/07/SDE21-RULES_V_2.1_29_06_21.pdf
SDE. (2022). SDE 21/22 Teams are the future. https://solardecathlon.eu/sde2122-teamsare-the-future/
University of Wuppertal. (2022). Herzlich Wilkommen beim Living Lab NRW. https://livinglabnrw.uni-wuppertal.de/de/
Voss, K., & Simon, K. (2022). Solar Decathlon Europe 21/22 - Competition Source Book (1st ed.). University of Wuppertal. https://doi.org/10.25926/svtg-e916
Appendix
SDE-2022 competition results: https://sdeurope.uni-wuppertal.de/en/competition/results/
Archive of previous Solar Decathlon projects: https://building-competition.org/
Related vocabulary
BIM
Design for Disassembly
Industrialised Construction
Area: Design, planning and building
Created on 16-02-2022
Read more ->Area: Design, planning and building
Created on 18-10-2023
Read more ->Area: Design, planning and building
Created on 09-11-2023
Read more ->Blogposts
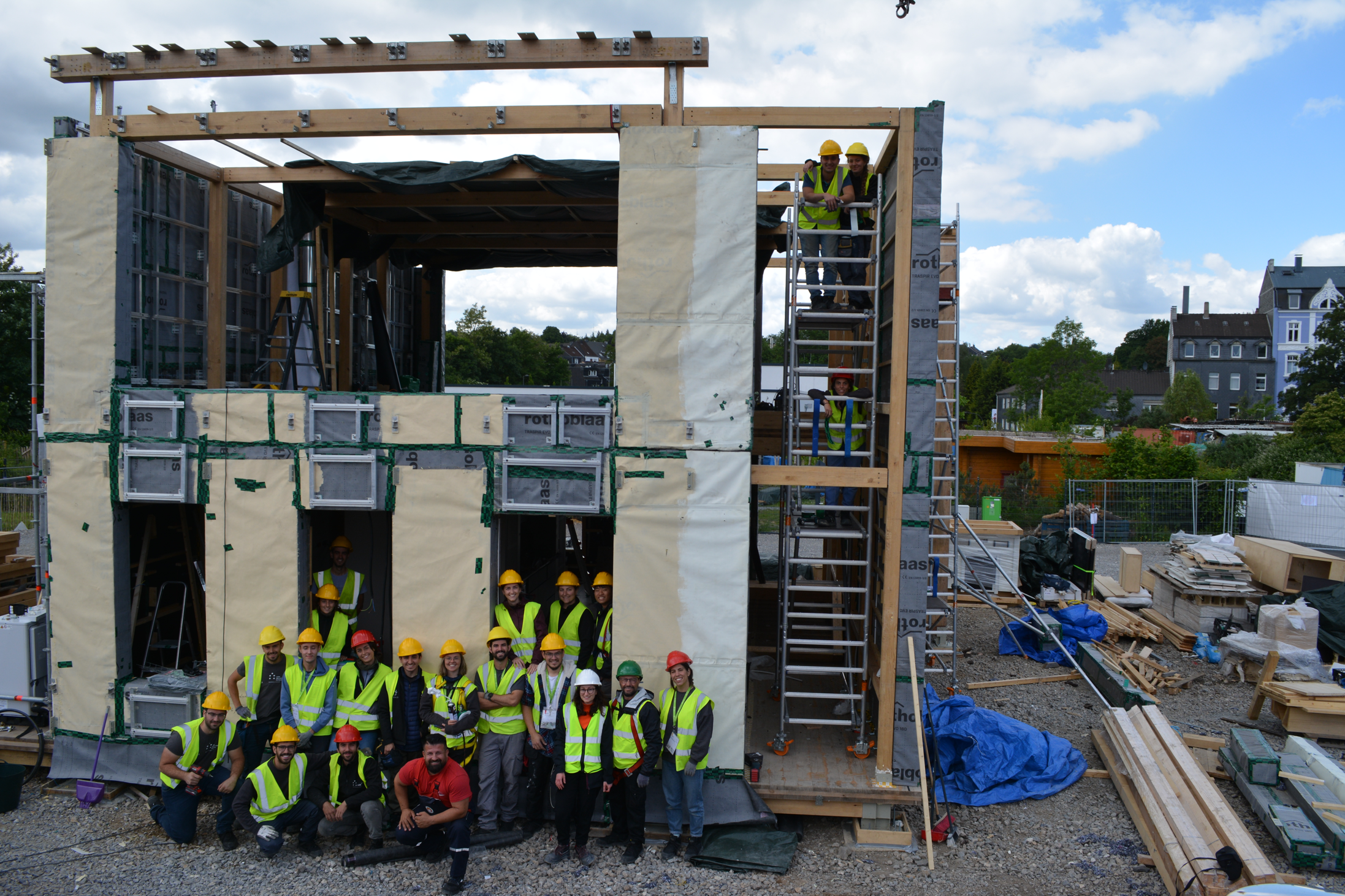
Solar Decathlon Competition and LCA | Secondment with UPV
Posted on 27-10-2022
Secondments
Read more ->