Barriers to re-warrantying building components
Created on 19-10-2023
Efficient re-warrantying of building components demands standardised protocols to streamline processes. The absence of such standards results in extensive and costly material testing, particularly for structural elements. Crucial stakeholders, including off-site manufacturers, insurers, and product suppliers (including second-hand product markets), are affected. To expedite the warranty process, the implementation of consistent guidelines and standardisation are vital tool. This strategic intervention reduces time and costs associated with testing individual materials, making the process more efficient. Employing scientific methods, such as in-depth interviews with experts and policy makers, provides valuable insights. Integrating these insights with standardised protocols enables the construction industry to surmount barriers, facilitating a smoother and more cost-effective re-warrantying process and making reuse more likely.
Systems knowledge
Actors
Housing developers
Non-profit and for-profit housing organisations that undertake various tasks, such as the construction and management of housing.
Architects and designers
Manufacturers
Method
Interviews
Interviews are structured or unstructured conversations between a researcher or interviewer and a participant or interviewee, designed to gather information, insights, or opinions on a particular topic or subject of study. Interviews are a common method in qualitative research for data collection and can be used in various research contexts.
Tools
Standardised protocol
Universally accepted set of rules and guidelines that ensures consistency and quality in a specific process or industry.
Target knowledge
Topic
Building regulations
A set of government-mandated standards, rules, and requirements that define how building and construction projects should be designed and executed.
Dimension
Institutional
The structure of government institutions that have the responsibility and power to create building regulation and monitor compliance with them
Level
Building
The structure, project or development that is directly impacted by the various building regulations.
Building product
Individual elements or parts that can be independently identified and evaluated within a larger building structure.
Transformation Knowledge
No references
Related vocabulary
Design for Disassembly
Area: Design, planning and building
Created on 18-10-2023
Read more ->Blogposts
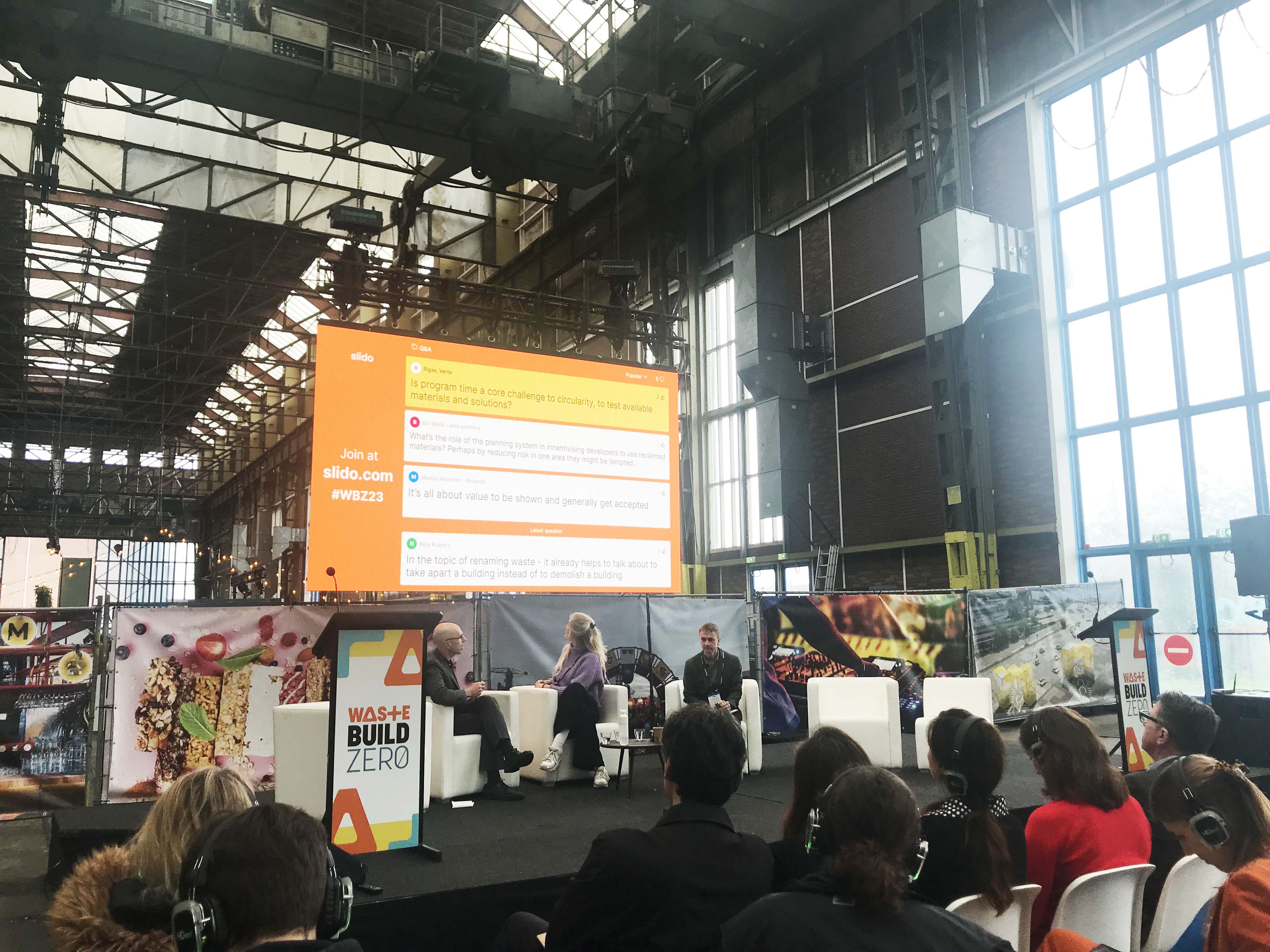
WasteBuild Zero conference in Amsterdam
Posted on 18-05-2023
Conferences, Secondments
Read more ->